Mastering the Art of Milling Delrin: A CNC Machining Guide
1 August 2024Preventative Measures to Avoid Costly Overhauls for Your Machining Spindle
5 August 2024
Have you ever wondered how intricate parts of machines or high-precision components are made with such accuracy? The answer lies in CNC machining—a technology that transforms design concepts into physical products with unparalleled precision. Without it, many of the advanced gadgets and machinery we rely on daily would be impossible to produce. If you're curious about the magic behind this technology, read on to discover how CNC machining works and why it's crucial in today’s manufacturing landscape.
CNC machining is a manufacturing process where pre-programmed computer software controls the movement of machinery and tools to cut, shape, and finish materials. This advanced technology enables the production of complex parts with exceptional precision and repeatability. By utilizing computer-aided design (CAD) and computer-aided manufacturing (CAM) software, CNC machining has revolutionized how we approach manufacturing, allowing for high efficiency and accuracy in creating a wide range of components.
Intrigued by how this sophisticated process unfolds? Let’s dive deeper into the world of CNC machining and explore its inner workings, advantages, and future trends.
Key Components of CNC Machining
Understanding CNC machining requires familiarity with its essential components. Each part plays a critical role in transforming digital designs into physical objects with precision and efficiency. Here's a detailed look at the key components involved in CNC machining:
CNC Machine: Parts and Functions
- Frame: The frame provides the structural support for the machine. It must be rigid and stable to ensure that vibrations do not affect the machining process. The stability of the frame is crucial for maintaining precision.
- Spindle: The spindle holds and rotates the cutting tool. Its speed and power are adjustable, allowing it to cut through various materials effectively. The spindle's performance directly impacts the quality of the finished product.
- Table: The table supports the workpiece and can move in multiple directions. Depending on the machine type, it may move along the X, Y, and Z axes to position the material accurately.
- Axes: CNC machines typically have multiple axes that control the movement of the tool and workpiece. Common configurations include three-axis (X, Y, Z) and more advanced multi-axis setups.
- Tool Holder: The tool holder secures the cutting tool in place. It must be precisely aligned to ensure accurate machining. Various types of tool holders are used depending on the machining requirements.
- Drive Motors: These motors control the movement of the axes. They are responsible for the precise positioning of the cutting tool and workpiece. Servo motors and stepper motors are commonly used in CNC machines.
Control Systems: Software and Hardware
- CNC Controller: The CNC controller is the brain of the machining process. It interprets the G-code (the programming language used for CNC machines) and directs the machine’s movements accordingly. Modern controllers are equipped with user-friendly interfaces and advanced features.
- Computer-Aided Design (CAD) Software: CAD software is used to create detailed 2D or 3D models of the parts to be machined. These models are crucial for generating accurate machining instructions.
- Computer-Aided Manufacturing (CAM) Software: CAM software converts the CAD designs into machine-readable instructions, often in the form of G-code. It helps in planning the tool paths and machining operations.
- User Interface: The user interface allows operators to interact with the CNC machine, input commands, and monitor the machining process. It may include a touchscreen, buttons, and display screens.
Tools and Workpieces: Types and Materials
- Cutting Tools: These tools come in various shapes and sizes, including drills, end mills, and lathes. They are selected based on the material being machined and the desired outcome. High-speed steel (HSS) and carbide are common materials for cutting tools.
- Workpieces: The material being machined, known as the workpiece, can be made from metals, plastics, composites, or wood. The choice of material affects the machining process and the tools used.
- Tooling Accessories: Accessories such as tool changers, collets, and chucks are used to hold and change tools during the machining process. They enhance the machine's versatility and efficiency.
- Workholding Devices: These devices, such as vices, clamps, and fixtures, secure the workpiece in place during machining. Proper workholding ensures stability and accuracy.
CNC machining is a sophisticated process that combines digital technology with mechanical precision to create detailed and accurate parts. The entire workflow—from design to finished product—involves several key stages. Here’s a step-by-step overview of how CNC machining operates:
The Design Process: CAD and CAM
Computer-Aided Design (CAD):
- Creating the Model: The process begins with creating a detailed digital model of the part using CAD software. This model includes precise dimensions, shapes, and features required for the final product. CAD software allows designers to visualize the part in 3D, making it easier to identify and correct design flaws before machining begins.
- Design Considerations: During the CAD phase, designers consider factors like material properties, tolerance requirements, and manufacturing constraints. This ensures that the design is practical and feasible for machining.
Computer-Aided Manufacturing (CAM):
- Generating Toolpaths: Once the CAD model is complete, CAM software converts the design into a set of instructions that the CNC machine can follow. These instructions, known as G-code, dictate how the machine should move, which tools to use, and how to cut the material.
- Simulation: CAM software often includes simulation features that allow operators to preview the machining process virtually. This helps in identifying potential issues and optimizing tool paths before actual production begins.
The Setup Process: Tooling and Workholding
Machine Setup:
- Loading the Program: The G-code generated by the CAM software is loaded into the CNC machine’s control system. This program contains all the necessary instructions for machining the part.
- Tool Selection: Based on the design and material, the appropriate cutting tools are selected and installed into the machine. Toolholders and adapters may be used to ensure proper fit and alignment.
- Workpiece Setup: Securing the Material: The workpiece is secured onto the machine’s table using workholding devices such as vices, clamps, or fixtures. Proper workholding is crucial for maintaining accuracy and preventing movement during machining.
- Aligning the Workpiece: The workpiece must be accurately aligned with the machine’s coordinate system. This alignment ensures that the machining operations are performed in the correct locations.
The Machining Process: Cutting, Drilling, and Milling
Cutting:
- Initial Cuts: The CNC machine begins by making rough cuts to remove excess material and shape the workpiece according to the design. This phase is focused on efficiency rather than precision.
- Finishing Cuts: After the rough cuts, finishing operations are performed to achieve the final dimensions and surface finish. Precision is critical in this phase to meet the design specifications.
Drilling:
- Drilling Holes: For parts requiring holes, the CNC machine uses specialized drills to create precise holes at specific locations. The machine’s control system ensures that the holes are drilled to the correct depth and diameter.
Milling:
- Milling Operations: Milling involves using rotary cutting tools to remove material from the workpiece. CNC milling machines can perform a variety of operations, including face milling, end milling, and contour milling, to achieve complex shapes and features.
Post-Processing: Quality Checks and Finishing
Inspection:
- Measuring Dimensions: After machining, the part is inspected to ensure it meets the design specifications. This may involve using precision measuring tools like calipers, micrometers, or coordinate measuring machines (CMM).
- Surface Finish: The surface finish of the part is evaluated to ensure it meets the required standards. Any necessary adjustments are made to address imperfections or improve the finish.
Finishing Operations:
- Deburring: The part may undergo deburring to remove sharp edges or residual material left from the machining process.
- Surface Treatments: Depending on the material and application, additional surface treatments such as polishing, coating, or painting may be applied to enhance the part’s appearance and durability.
CNC machines come in various types, each designed for specific applications and manufacturing processes. Understanding the different types helps in selecting the right machine for a particular task and optimizing the production workflow. Here’s an overview of the main types of CNC machines:
- CNC Milling Machines:
- Vertical and Horizontal: Used for cutting and shaping materials with high precision. Vertical mills are ideal for flat surfaces, while horizontal mills handle heavier and bulkier parts.
- CNC Turning Machines:
- Lathes and Turning Centers: Focus on rotating the workpiece while cutting tools shape it. Lathes are used for cylindrical parts, and turning centers add additional capabilities like milling.
- CNC Routers:
- Wood and Plastic Cutting: Ideal for large sheets and intricate designs, commonly used in woodworking and sign-making.
- CNC Plasma Cutters:
- Metal Cutting: Employ a plasma torch for precise cuts in conductive materials like steel and aluminum.
- CNC Laser Cutters:
- High Precision Cutting: Utilize a focused laser beam to cut or engrave materials with high accuracy, suitable for detailed patterns and complex shapes.
Advantages of CNC Machining
CNC machining offers numerous benefits that make it a preferred choice for modern manufacturing. The technology's precision, efficiency, and versatility address many of the challenges faced in traditional manufacturing methods. Here’s an in-depth look at the key advantages of CNC machining:
Precision and Accuracy
High Tolerance:
- Description: CNC machines are capable of achieving extremely tight tolerances, often within microns. This level of precision ensures that each part is manufactured to exact specifications, which is crucial for applications where even minor deviations can impact performance.
- Impact: High tolerance levels contribute to the reliability and consistency of the final product, making CNC machining ideal for complex and high-precision components.
Repeatability:
- Description: Once a CNC machine is programmed, it can reproduce the same part with consistent accuracy, regardless of the number of units produced. This repeatability is essential for high-volume production runs.
- Impact: Consistent quality across multiple parts ensures uniformity and reduces the need for extensive quality control checks.
Efficiency and Productivity
Reduced Production Time:
- Description: CNC machines can perform multiple operations in a single setup, such as cutting, drilling, and milling, significantly reducing production time. Automated tool changes and rapid processing speeds contribute to faster manufacturing.
- Impact: Shorter production cycles lead to increased output and quicker turnaround times, which can enhance overall productivity.
Minimized Human Error:
- Description: By automating the machining process, CNC technology reduces the reliance on manual labor and minimizes the potential for human error. This leads to more reliable and accurate results.
- Impact: Reduced errors lower the likelihood of defective parts and the associated costs of rework or scrap.
Versatility and Flexibility
Wide Range of Materials:
- Description: CNC machines can work with various materials, including metals, plastics, composites, and wood. This versatility makes them suitable for a broad spectrum of applications and industries.
- Impact: The ability to machine different materials with the same equipment enhances the machine's utility and allows for diverse product offerings.
Complex Geometries:
- Description: CNC machining can produce intricate shapes and complex geometries that would be challenging or impossible with manual methods. The advanced capabilities of CNC machines allow for detailed and precise designs.
- Impact: This flexibility enables the production of highly specialized parts and components tailored to specific requirements.
Reduced Labor Costs
Automation:
- Description: CNC machines operate with minimal human intervention, allowing one operator to manage multiple machines simultaneously. Automation reduces the need for manual labor and associated costs.
- Impact: Lower labor costs contribute to overall cost savings and increased profitability.
Less Skill Required:
- Description: While operating CNC machines requires technical knowledge, the level of skill needed is less compared to traditional machining methods. Once the machine is set up and programmed, the actual operation is relatively straightforward.
- Impact: Reduced skill requirements facilitate training and reduce labor costs associated with highly skilled machinists.
Enhanced Safety
Enclosed Work Environment:
- Description: CNC machines are typically enclosed, protecting operators from exposure to hazardous cutting tools and flying debris. The automated nature of the machines also reduces direct interaction with the machining process.
- Impact: Improved safety features help prevent workplace accidents and injuries.
Consistent Quality Control:
- Description: CNC machines are equipped with sensors and feedback systems that monitor the machining process and ensure quality. These systems can detect deviations and adjust the process accordingly.
- Impact: Enhanced quality control reduces the likelihood of defective parts and ensures consistent product standards.
Applications of CNC Machining
CNC machining's versatility and precision make it indispensable across various industries. Its ability to produce complex and accurate parts efficiently has led to widespread adoption in numerous fields. Here’s a detailed look at some of the key applications of CNC machining:
- Aerospace: CNC machining produces essential parts such as engine components and structural elements for aircraft and spacecraft. Its accuracy ensures the reliability and performance of aerospace vehicles.
- Automotive: In the automotive sector, CNC machines create engine components, transmission parts, and custom prototypes. This technology enhances vehicle performance, enables rapid development, and supports high-volume production.
- Medical Devices: CNC machining is crucial for manufacturing precision surgical instruments and custom implants. The ability to work with medical-grade materials and achieve tight tolerances supports the creation of high-quality medical devices.
- Consumer Electronics: CNC machines are used to fabricate enclosures, housings, and internal components for electronic devices. The technology ensures high-quality finishes and accurate features, which are vital for the performance and aesthetics of consumer electronics.
- Industrial Equipment: CNC machining produces various components for industrial machinery, including machine tools, conveyors, and pumps. It enhances the functionality and efficiency of equipment, contributing to improved manufacturing processes and productivity.
Challenges and Considerations in CNC Machining
While CNC machining offers numerous advantages, it also comes with its own set of challenges and considerations. Addressing these issues is crucial for optimizing the machining process and achieving the desired results. Here’s a detailed look at the key challenges and factors to consider in CNC machining:
Initial Costs and Maintenance
High Initial Investment:
- Description: CNC machines and associated equipment represent a significant capital investment. The cost of purchasing high-quality machines, software, and tools can be substantial.
- Impact: The high upfront costs can be a barrier for smaller businesses or startups. However, the long-term benefits and efficiency gains often justify the initial expenditure.
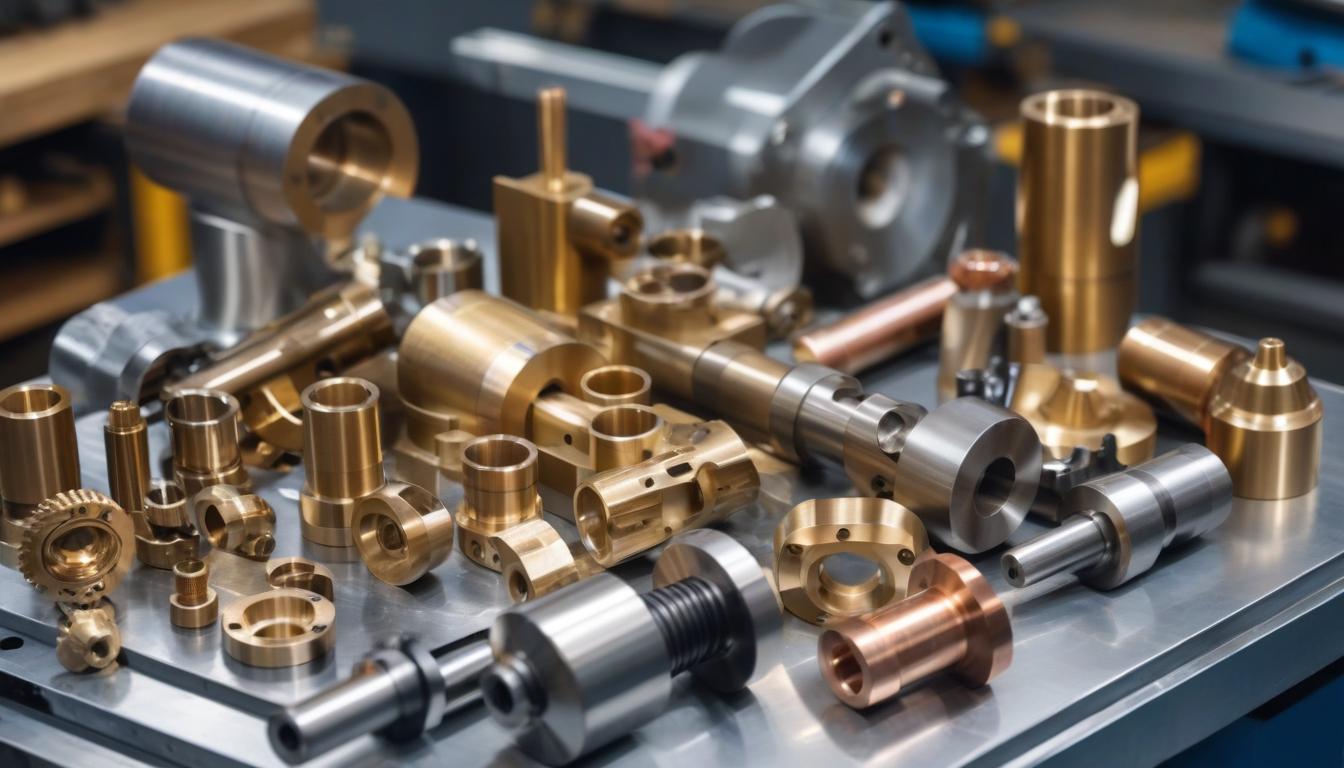
Maintenance Requirements:
- Description: Regular maintenance is essential to keep CNC machines in optimal working condition. This includes routine checks, cleaning, calibration, and replacement of worn parts.
- Impact: Maintenance can incur additional costs and requires dedicated resources. Neglecting maintenance can lead to reduced machine performance and increased downtime.
Material Limitations
Material Compatibility:
- Description: Not all materials are suitable for CNC machining. Certain materials, such as very hard metals or highly abrasive substances, may require specialized tools or machines.
- Impact: Material limitations can affect the choice of machine and tooling, potentially increasing costs or limiting the range of parts that can be produced.
Tool Wear and Replacement:
- Description: Hard or abrasive materials can cause faster wear and tear on cutting tools. Frequent tool replacement or sharpening may be necessary.
- Impact: Increased tool wear can lead to higher operational costs and more frequent maintenance. It also requires careful management of inventory and tool life.
Skill Requirements and Training
Operator Skill Levels:
- Description: Operating CNC machines requires a certain level of technical skill and knowledge. Operators must be proficient in programming, machine setup, and troubleshooting.
- Impact: Skilled operators are essential for achieving high-quality results. Recruiting or training qualified personnel can be a challenge and may involve additional costs.
Continuous Learning:
- Description: As technology evolves, operators need to stay updated with the latest advancements in CNC machining, software, and techniques.
- Impact: Ongoing training and professional development are necessary to maintain proficiency and adapt to new technologies. This can be time-consuming and costly.
Environmental and Safety Concerns
Waste Management:
- Description: CNC machining processes generate material waste, including chips and swarf. Proper disposal and recycling of this waste are essential for environmental sustainability.
- Impact: Effective waste management practices are required to minimize environmental impact and comply with regulations. This may involve additional costs and logistical considerations.
Safety Risks:
- Description: Although CNC machines are generally safer than manual machinery, there are still risks associated with their operation, such as exposure to sharp tools, high-speed spindles, and flying debris.
- Impact: Implementing safety protocols and protective equipment is necessary to ensure a safe working environment. Proper training and adherence to safety standards help mitigate risks.
Technical and Operational Challenges
Programming Complexity:
- Description: CNC programming involves creating precise G-code instructions for the machine. Complex parts and intricate designs can make programming challenging.
- Impact: Developing and debugging G-code can be time-consuming and requires a deep understanding of both the design and machining processes.
Machine Calibration and Alignment:
- Description: Accurate machining depends on proper machine calibration and alignment. Any deviations can result in defects or inaccuracies in the final part.
- Impact: Regular calibration and alignment checks are necessary to maintain precision. Addressing misalignments or errors can require specialized skills and tools.
CNC machining stands as a cornerstone of modern manufacturing, offering unmatched precision, efficiency, and versatility. As we move into 2024, the integration of advanced technologies like IoT, AI, and hybrid manufacturing methods promises to further elevate the capabilities of CNC machines. While challenges such as high initial costs and material limitations persist, ongoing innovations in automation, sustainability, and design tools continue to drive the industry forward. Embracing these trends will not only optimize production processes but also position manufacturers at the forefront of technological advancement, ensuring a competitive edge in the ever-evolving landscape of manufacturing.